
Pragmatisches Bestimmen der Kritikalität von Lieferanten und deren Bauteilen Risikomanagement in der Supply Chain
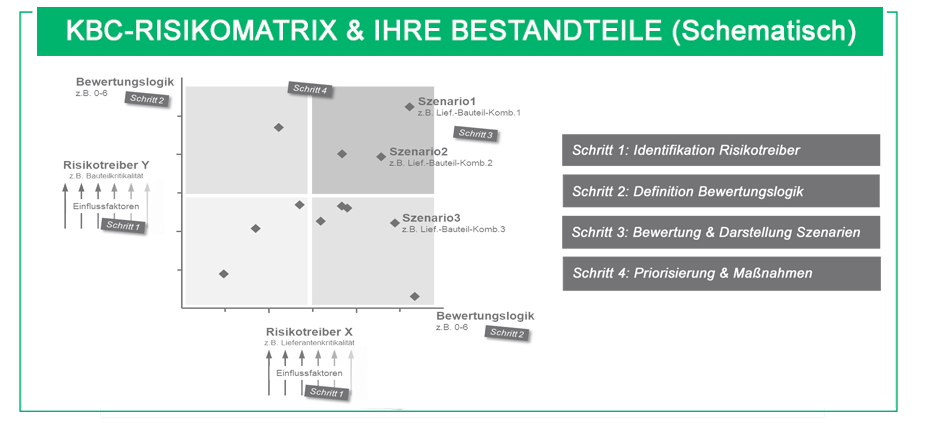
Mit der Risikomatrix von Jonathan Isele und Max Weidmann lassen sich selbst mehrere hundert Lieferanten-Bauteil-Kombinationen übersichtlich darstellen, um Risiken hinsichtlich Lieferantenzuverlässigkeit und Bauteilqualität einschätzen zu können.
Management Summary
Als Mitglied erhalten Sie die wichtigsten Thesen des Beitrags zusammengefasst im Management Summary!
Inhalt
- Ansteigende Qualitätskosten bei unzureichendem Risikomanagement
- Die methodische Erarbeitung der KBC Risikomatrix in vier Schritten
- Schritt 1: Identifikation Risikotreiber
- Schritt 2: Definition Bewertungslogik
- Schritt 3: Bewertung & Darstellung der Szenarien
- Schritt 4: Priorisierung & Maßnahmen
- Zusammenfassung & Ausblick
Pragmatisches Bestimmen der Kritikalität von Lieferanten und deren Bauteilen Risikomanagement in der Supply Chain
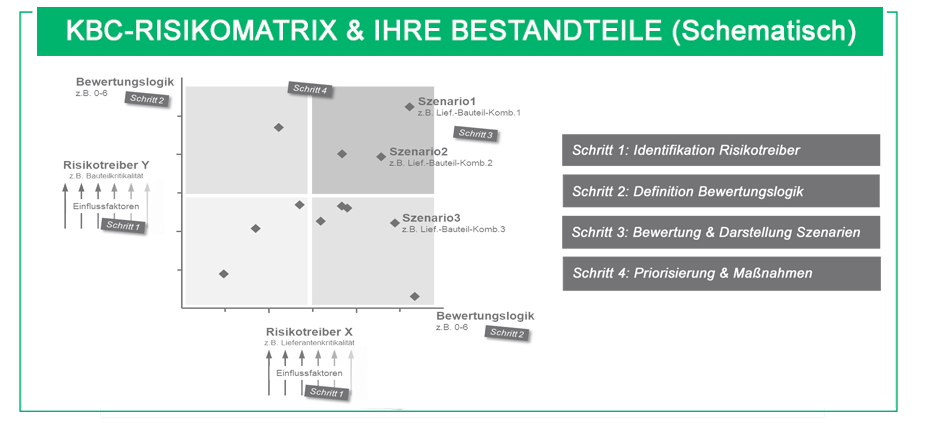
Mit der Risikomatrix von Jonathan Isele und Max Weidmann lassen sich selbst mehrere hundert Lieferanten-Bauteil-Kombinationen übersichtlich darstellen, um Risiken hinsichtlich Lieferantenzuverlässigkeit und Bauteilqualität einschätzen zu können.
Management Summary
Als Mitglied erhalten Sie die wichtigsten Thesen des Beitrags zusammengefasst im Management Summary!
Inhalt
- Ansteigende Qualitätskosten bei unzureichendem Risikomanagement
- Die methodische Erarbeitung der KBC Risikomatrix in vier Schritten
- Schritt 1: Identifikation Risikotreiber
- Schritt 2: Definition Bewertungslogik
- Schritt 3: Bewertung & Darstellung der Szenarien
- Schritt 4: Priorisierung & Maßnahmen
- Zusammenfassung & Ausblick
Industrieunternehmen stehen heutzutage vor vielen Herausforderungen: Die fortschreitende Globalisierung und der damit verbundene Kostendruck sowie die ausbreitende Digitalisierung von Produkten und Produktionsprozessen sind nur zwei Beispiele hierfür. Neben immer kürzer werdenden Produktlebenszyklen steigen sowohl Kundenanforderungen als auch Variantenvielfalt und Produktkomplexität. So müssen zahlreiche Produkte in immer kürzerer Zeit kostenoptimal entwickelt und auf den Markt gebracht werden. Dies erfordert Supply Chains, in denen die jeweiligen Unternehmen über Landesgrenzen hinweg eng miteinander verknüpft sind und effizient agieren.
Nach einer Studie von Bendul und Brüning kommt es innerhalb solcher Supply Chains regelmäßig zu mittleren oder schwerwiegenden Störungen. Unterbrechungen in Material- oder Informationsfluss können demnach die Produktivität oder den Umsatz senken – und zwar unabhängig von der Branche.
Für Unternehmen stellen Störungen in den Supply Chains hohe Risiken dar, denen häufig mit dem Aufbau von Sicherheitsbeständen oder dem Unterhalt eines möglichst breiten und nachhaltig stabilen Lieferantenportfolios entgegengewirkt wird. Die klassischen Maßnahmen des Risikomanagements in der Supply Chain führen dabei zu einem sehr hohen Kosten- und Koordinierungsaufwand.
Zum Erhalt ihrer Wettbewerbsfähigkeit müssen Unternehmen heute die begrenzten Ressourcen (finanzielle Mittel, Personal etc.) möglichst effizient und effektiv einsetzen. Dieser Optimierungsdruck steht den oben genannten Maßnahmen des Risikomanagements gegenüber. Die optimierten und schlanken Supply Chains (reduzierte Sicherheitsbestände, konsolidierte und kostenoptimierte Lieferantenstruktur etc.) bergen eine Vielzahl an Risiken, die in der heutigen volatilen Umwelt kaum mehr wirtschaftlich abzusichern sind.
Durch die enge Kopplung von Supply Chains nach dem Just-In-Sequence Prinzip können auch kleinste Vorfälle erhöhte Kosten, Qualitätsprobleme oder Versorgungsengpässe für die gesamte Wertschöpfungskette bedeuten. So führen Qualitätsmängel bei einem nachgelagerten Lieferanten (n-Tier) möglicherweise zu Qualitätsproblemen und Produktionsausfällen beim Original Equipment Manufacturer (OEM). Folgen davon sind qualitätsbedingte Rückrufaktionen und verzögerte Auslieferungen mit entsprechendem Image-Schaden und Regressforderungen an betroffene Lieferanten. Die Herausforderung des Risikomanagements besteht darin, Supply Chain Risiken für das Unternehmen möglichst umfangreich zu managen und zeitgleich kostenoptimiert zu agieren.
Ansteigende Qualitätskosten bei unzureichendem Risikomanagement
Genau diesem Spannungsfeld – maximale Risikoreduzierung bei beschränktem Ressourceneinsatz – sah sich ein Automotive-OEM und Kunde der Unternehmensberatung Kemény Boehme & Company (KBC) gegenüber: Ein deutlicher Anstieg an lieferanteninduzierten Qualitätskosten deckte Mängel im Supply Chain Risikomanagement auf. Vor dem Hintergrund beschränkter personeller und finanzieller Ressourcen sollte ein ganzheitlicher und systematischer Ansatz zum Risikomanagement erarbeitet werden. Im dafür beauftragten Projekt kamen die beiden KBC Berater Jonathan Isele und Max Weidmann beim Kunden an der Schnittstelle zwischen Einkauf und Qualitätsmanagement zum Einsatz.
Ziel des Projektes war die Entwicklung eines Ansatzes zur Identifizierung, Bewertung und Priorisierung von Risiken entlang der Supply Chain. Dieser sollte den effizienten und zielgerichteten Einsatz von Ressourcen ermöglichen. Die umfangreiche und vernetzte Supply Chain des Kunden, die über 500 Lieferanten im In- und Ausland sowie entsprechende Sublieferanten-Strukturen umfasste, erschwerte die Aufgabenstellung zusätzlich.
Die methodische Erarbeitung der KBC Risikomatrix in vier Schritten
KBC hat eine Methode entwickelt, die diesen Herausforderungen gerecht wird. Sie setzt sich aus vier aufeinander aufbauenden Schritten zusammen und ist auf verschiedenste Anwendungsfälle übertragbar. Die Herangehensweise wird im Folgenden Schritt für Schritt generisch sowie anhand des konkreten Fallbeispiels mit dem Automotive-OEM beschrieben. Das Ergebnis ist eine Risikomatrix, welche sowohl die Lieferanten- als auch die entsprechende Bauteilkritikalität abbildet.
Schritt 1: Identifikation Risikotreiber
Zunächst sind die relevanten Risikotreiber zu identifizieren. Hierfür werden Aspekte definiert, die die jeweiligen Eigenschaften der Risiken beschreiben. Im klassischen Risikomanagement werden die möglichen Szenarien häufig bezüglich ihrer Eintrittswahrscheinlichkeit und (finanziellen) Auswirkung betrachtet. In der Praxis ist jedoch meist eine umfassendere Risikobetrachtung notwendig.
Im Anwendungsfall war die reine Betrachtung des Ausfallrisikos eines Lieferanten ebenfalls nicht ausreichend. Im Falle des OEM stellten die Lieferanten erst in Kombination mit den jeweils gelieferten Bauteilen die zentralen Risikotreiber dar. So verkörperte ein „kritischer Lieferant“ erst dann ein nennenswertes Risiko für das Unternehmen, sofern seine Bauteile für das Endprodukt als entsprechend kritisch eingestuft wurden. Die Risikotreiber waren wiederum von noch zu definierenden Einflussfaktoren abhängig. Bild 1 zeigt eine schematische Darstellung zur Identifikation von Risikotreibern und deren Einflussfaktoren.
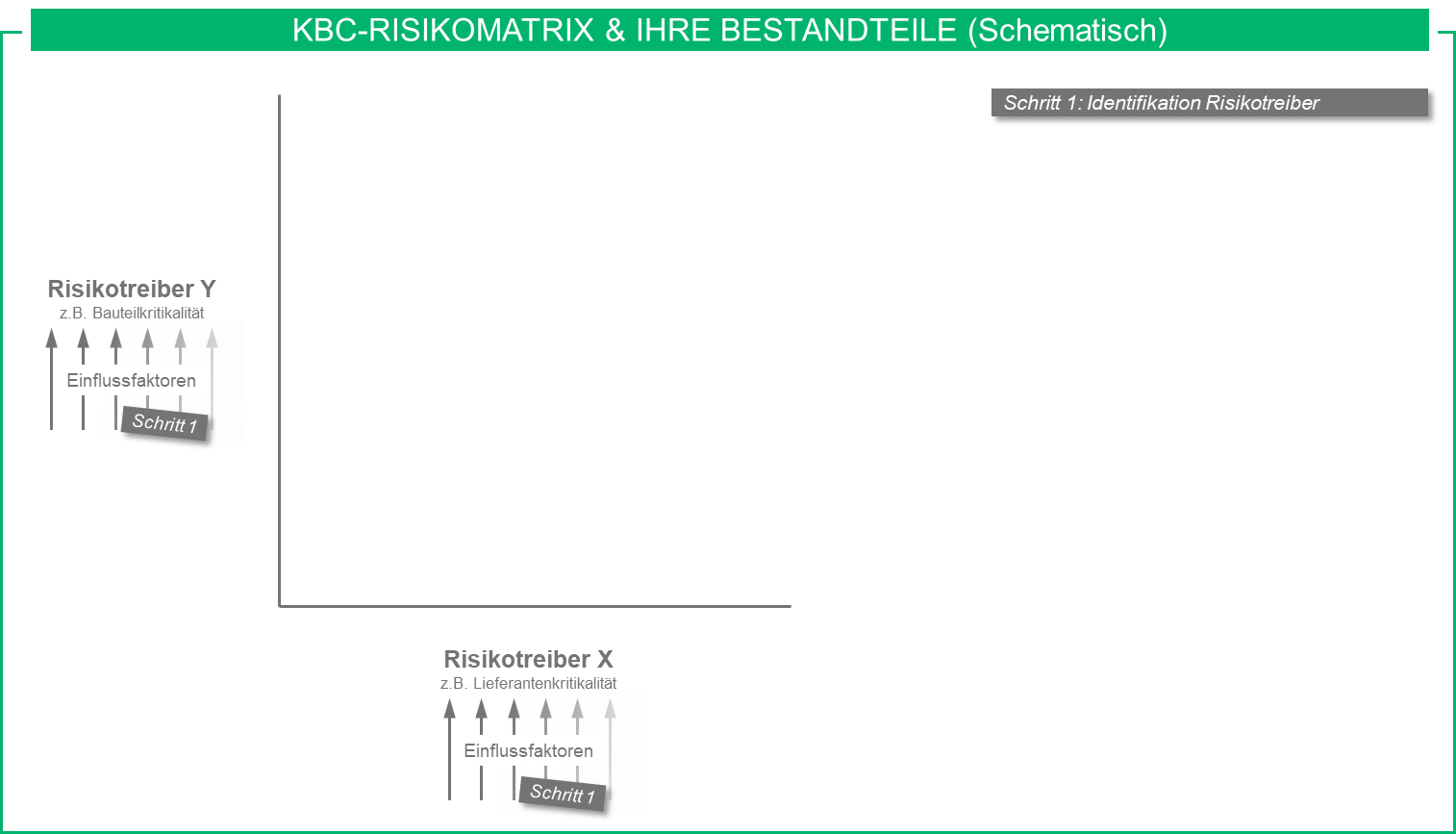
Sofort weiterlesen und testen
Erster Monat kostenlos,
dann 24,95 € pro Monat
-
Know-how von über 1.000 Profis
-
Methoden für alle Aufgaben
-
Websessions mit Top-Expert:innen