
Kanban
Kanban (jap.: Karte, Signalkarte) ist eine Methode zur dezentralen, selbstorganisierenden Steuerung von Materialflüssen in Fertigungsprozessen. Sie ist Grundlage der Just-in-Time-Produktion.
Kanban
Kanban (jap.: Karte, Signalkarte) ist eine Methode zur dezentralen, selbstorganisierenden Steuerung von Materialflüssen in Fertigungsprozessen. Sie ist Grundlage der Just-in-Time-Produktion.
Mit der Kanban-Methode steuert ein Team seine Prozesse oder Aufgaben. Dazu nutzt das Team ein Board (Kanban, japanisch: Karte, Signalkarte), auf dem Spalten den Bearbeitungsstand einer Aufgabe visualisieren und die einzelnen Aufgaben auf Karten über das Board wandern. Ein Kanban-Board hat mindestens drei Spalten: Offen (To Do), in Bearbeitung (Doing) und Erledigt (Done).
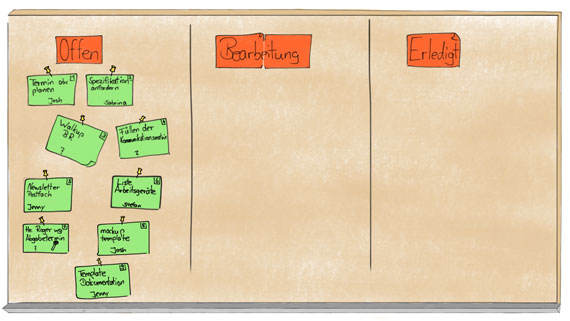
© Daniel Reinold
Kanban in Projekten
Insbesondere bei Software-Entwicklungsprojekten ist es möglich, Kanban auch auf die Steuerung der Projektarbeit anzuwenden. Hierbei stellen die Aufgaben (bzw. Arbeitspakete) den Materialfluss dar. Jede Aufgabe erhält eine (reale oder virtuelle) Karte, die einer bestimmten Entwicklungsstufe zugeordnet wird (z.B.: Entwicklung, Test).
Sobald ein Arbeitsteam eine Aufgabe erledigt hat, holt es sich selbständig die nächste Aufgabe aus dem entsprechenden Kartenpool (siehe Software-Kanban – eine Einführung). Der Vorteil für die Projektarbeit liegt darin, dass der Managementaufwand reduziert und die Abarbeitungsgeschwindigkeit steigt.
Voraussetzung für die Verwendung von Kanban für die Aufgabensteuerung in Projekten ist, dass die Arbeitspakete in zwar aufeinanderfolgende, aber ansonsten unabhängige Arbeitsschritte gegliedert werden können.
Herkunft
Im Rahmen des Toyota Produktionssystems (TPS) entwickelte der Japaner Taiichi Ohno die Regeln und Prozesse von Kanban. Grundprinzip von Kanban ist die Organisation eines mehrstufigen Produktionsprozesses in verknüpfte Regelkreise, die jeweils aus einer Fertigungsstufe und einem vorgelagerten Materiallager (Puffer) bestehen. Jeder Fertigungsprozess entnimmt seinem Materiallager die momentan benötigte Materialmenge. Die vorgelagerte Fertigungsstufe füllt selbständig, d.h. ohne zentrale Aufforderung, die dadurch entstandene Lücke im Materiallager auf. Entnahme und Fertigung werden mit Hilfe entsprechender Karten dokumentiert, woraus sich auch die Namensgebung von Kanban ableitet. Während sich der Materialfluss somit von Rohmaterial bis zum Endprodukt bewegt, fließt die Information umgekehrt von der letzten zur ersten Produktionsstufe.
Auf diese Weise entsteht ein sich selbst organisierendes System, das einerseits möglichst geringe Lagerhaltung benötigt und andererseits die Fertigungskapazitäten stets auf den aktuellen Engpass konzentriert. (Zollondz, Hans-Dieter: Lexikon Qualitätsmanagement, 2001; Kamiske, Gerd F. u. Brauer, Jörg-Peter: Qualitätsmanagement von A bis Z, 2003)