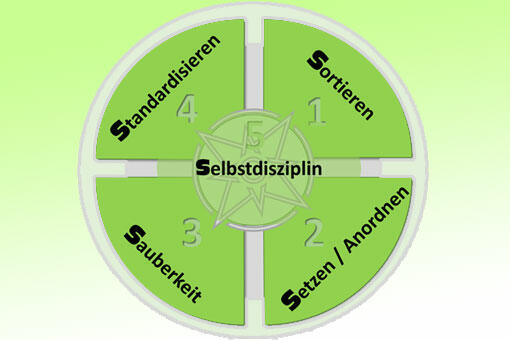
5S-Methode für KVP
5S ist eine elementare Methode des Qualitätsmanagements und des Lean Managements. Die fünf Schritte Sortieren, Setzen / Anordnen, Sauberkeit, Standardisieren und Selbstdisziplin beschreiben einen kontinuierlichen Prozess, um Effizienz zu erhöhen, weniger Ressourcen zu verschwenden und die Qualität des Arbeitsergebnisses zu verbessern. In der zielgerichteten Anwendung wird der kontinuierliche Verbesserungsprozess (KVP) von den beteiligten Personen getragen und gelebt; dadurch wird er nachhaltig und dauerhaft wirksam.
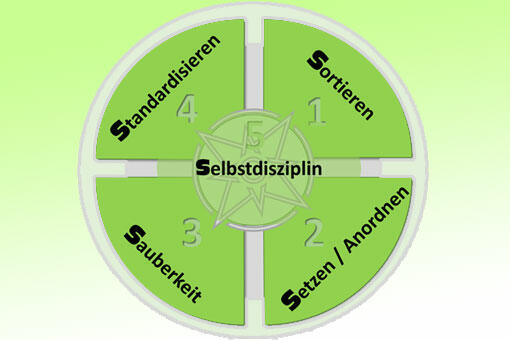
5S-Methode für KVP
5S ist eine elementare Methode des Qualitätsmanagements und des Lean Managements. Die fünf Schritte Sortieren, Setzen / Anordnen, Sauberkeit, Standardisieren und Selbstdisziplin beschreiben einen kontinuierlichen Prozess, um Effizienz zu erhöhen, weniger Ressourcen zu verschwenden und die Qualität des Arbeitsergebnisses zu verbessern. In der zielgerichteten Anwendung wird der kontinuierliche Verbesserungsprozess (KVP) von den beteiligten Personen getragen und gelebt; dadurch wird er nachhaltig und dauerhaft wirksam.
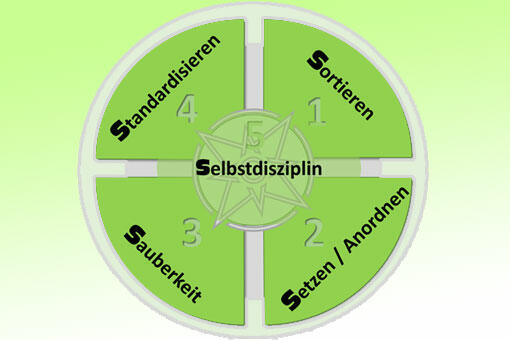
Einsatzmöglichkeiten
- Optimierung von Arbeitsumgebungen aller Art, von Schreibtisch bis zur Produktionshalle
- Optimierung von Produktionsprozessen aller Art einschließlich der Qualitätssteuerung (z.B. Zusammenbau, Fertigung, Prüflabor)
- Optimierung digitaler und virtueller Abläufe wie z.B. in Kollaborationsplattformen, Serverlandschaften, Homeoffice oder Programmierumgebungen.
- Erhöhung der Effizienz, Reduktion von Bearbeitungszeiten und Steigerung der Qualität bei Büroarbeit sowohl am Schreibtisch als auch für Aufbau und Durchführung von Besprechungen
5S kann sowohl von Einzelpersonen als auch von Gruppen durchgeführt werden. In der Regel sind 5S-Gruppenworkshop wirksamer, da wertvolle Impulse von mehreren Beteiligten einfließen. Zudem stärken Workshops das Wir-Gefühl, das dabei hilft, die Verbesserungsmaßnahmen nachhaltiger zu gestalten.
Ergebnisse
- Der betrachtete Arbeitsbereich ist frei von nicht benötigten, behindernden Elementen. "Elemente" können dabei sowohl reale Gegenstände als auch virtuelle Dinge (z.B. Prozesse) sein.
- Alle benötigten Werkzeuge haben einen festen Platz und funktionieren einwandfrei. "Werkzeuge" können dabei z.B. ebenfalls sein: Software, Computer, Schnittstellen oder Kommunikationswege.
- Maßnahmen zur Standardisierung der Abläufe sind definiert.
- Ein überwachter Verbesserungsprozess ist etabliert, um den betrachteten Arbeitsbereich kontinuierlich in kleinen Schritten weiter zu optimieren.
Das wichtigste Ergebnis der 5S-Methode ist der gelebte kontinuierliche Verbesserungsprozess. Um es mit einem Bild auszudrücken: Das einmalige Aufräumen eines Kinderzimmers löst das Chaosproblem nur für eine (sehr) kurze Zeit.
Vorteile
Durchführung: Schritt für Schritt
Websession
Sand im Prozessgetriebe? Mit SIPOC finden Sie heraus, wo es hakt!
Genial einfach und verblüffend wirkungsvoll: Mit der SIPOC-Analyse erhalten Sie ein Universalwerkzeug zur Fehlersuche in Prozessen.
Die 5S-Methode (Bild 1) stammt aus der industriellen Produktion und ist grundlegender Bestandteil des Toyota-Produktionssystems. Sie lässt sich aber auch hervorragend auf andere Bereiche wie z.B. das Büroumfeld oder sogar den privaten Bereich anwenden. Je mehr Mitmenschen an einem Platz arbeiten, desto höher ist deren Interaktion miteinander, so dass in der 5S-Methodik auch Hinweise zu standardisierten Abläufen und Nachhaltigkeit von Maßnahmen enthalten sind. Wichtig ist dabei, dass sich jeder einbringen kann und soll, um den kontinuierlichen Verbesserungsprozess aufrechtzuerhalten.
Erfolgreich wird das System, wenn seine Methodik gelebt wird, Verbesserungen in kleinen Schritten erzielt werden und aus diesen dann neue Standards erwachsen.
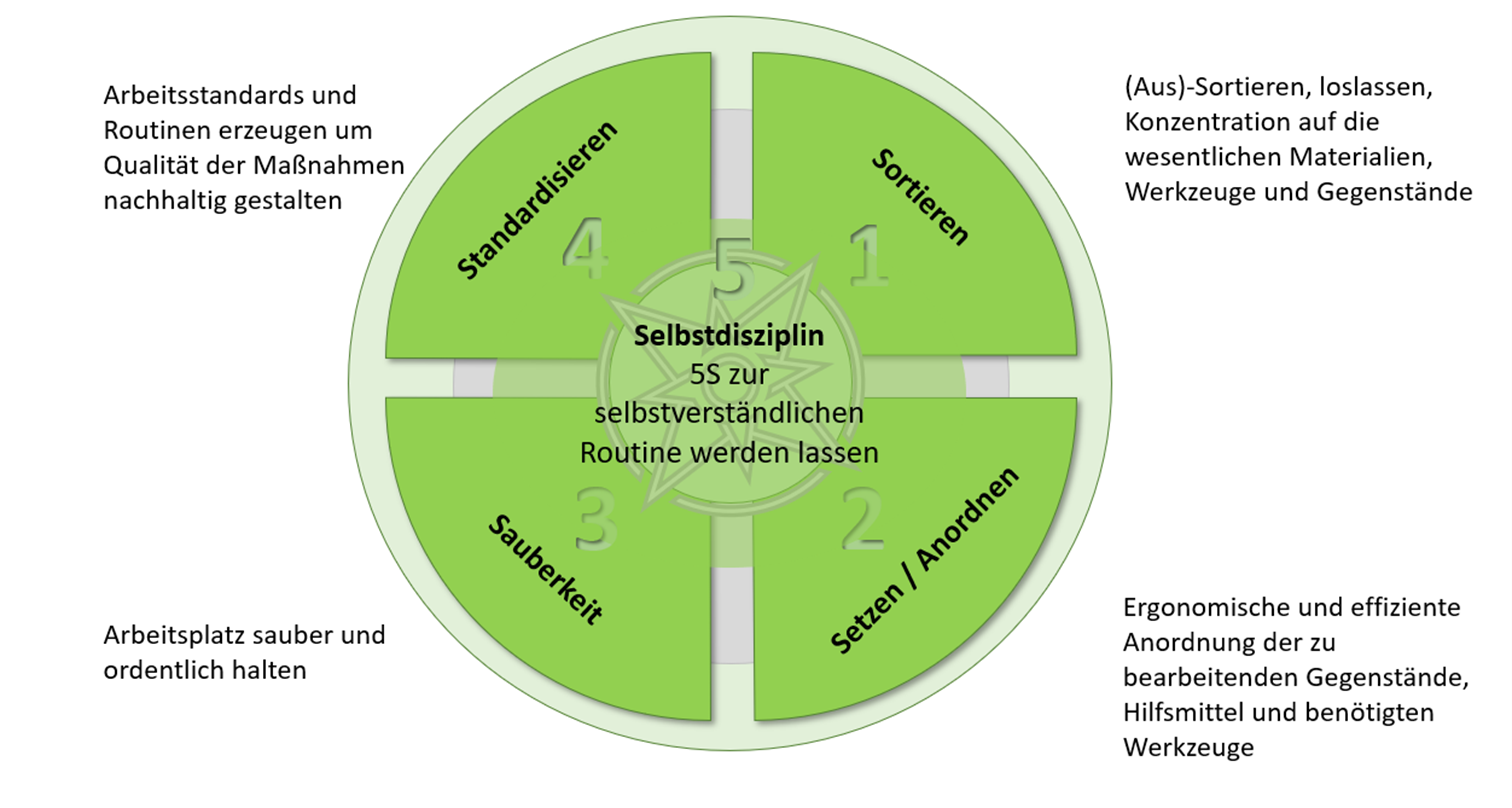
Isoliert betrachtet finden sich in einem Arbeitsbereich zwar immer wieder Ansatzpunkte, Abläufe neu zu strukturieren und eine günstigere Umgebung zu gestalten. Richtig angewandt führen die Bausteine der Methode aber zu einer kontinuierlichen Verbesserung der räumlichen Situation und zu einem störungsfreien Arbeitsablauf.
Jede Nacharbeit und arbeitsplatzbedingte Zusatzarbeit wird im Toyota-Produktionssystem als Verschwendung von Ressourcen angesehen. Diese Ressourcenverschwendungen werden dort in drei Kategorien zusammengefasst: Ausschuss, Ungleichgewicht und Überbeanspruchung (Bild 2).

Wird beispielhaft in einem chaotischen Umfeld produziert, so führen die Umstände angefangen von Einflüssen durch Unordnung wie "Suchen von Werkzeugen", "Beschädigung durch unsachgemäße Ablagen", "Schlechte Qualität durch Unsauberkeit" zu einem unstrukturierten Ablauf, der leicht ins Ungleichgewicht driften kann. Dies führt dann unweigerlich zu Hektik und Überbeanspruchung bei gleichzeitigem Qualitätsverlust.
Hierbei gilt es, durch Ordnung und Sauberkeit Arbeitsplätze und Bereiche sicherer und übersichtlicher zu gestalten. Transport- und Wartezeiten sowie umgebungsbedingte Qualitätsmängel sollen nachhaltig reduziert werden. Genauso wird das Risiko für Arbeitsunfälle vermindert oder sogar eliminiert (Poka Yoke, s.u.).
Es handelt sich hierbei um allgemeine Prinzipien, die in gleicher Weise für eine Arbeitssituation wie für einen Kinderspielplatz gelten: Ihren Zweck können sie umso besser erfüllen, je mehr sie an der 5S-Methodik ausgerichtet werden.
Im Deutschen bemüht man sich mit Übersetzungen der 5S Methode, die den Anfangsbuchstaben "S" der ursprünglichen japanischen Bezeichnungen beibehalten. Parallel dazu gibt es auch Übersetzungen, bei denen der Anfangsbuchstabe "A" verwendet wird, so dass synonym von der "5A-Methode" gesprochen wird. Für beide Übersetzungen sind verschiedene Versionen im Umlauf.
5S (Japanisch) |
5S (Deutsch) |
5A (Deutsch) |
Seiri |
Sortieren |
Aussortieren |
Seiton |
Setzen und Anordnen |
Aufräumen / Arbeitsmittel ergonomisch anordnen |
Seiso |
Sauberkeit / Säubern |
Arbeitsplatzsauberkeit |
Seiketsu |
Standardisieren |
Anordnung zur Regel machen |
Shitsuke |
Selbstdisziplin |
Alle Punkte einhalten und verbessern |
Aus Gründen der einfacheren Lesbarkeit wird im Folgenden meist die grammatikalisch männliche Form (Mitarbeiter usw.) verwendet. Es sind dabei aber stets Personen jeden Geschlechts gemeint.
Vorbereitung: Führen Sie eine Bestandsaufnahme durch!
Für die Bestandsaufnahmen sollten Sie sich ein Bild vom Ort des Geschehens machen. Machen Sie den "Gemba-Walk", gehen Sie also dorthin, wo die Arbeit geschieht und machen Sie sich dort selbst ein Bild aus erster Hand. Informieren Sie hierzu ggf. den Betriebsrat über Ihr Vorhaben und beachten Sie selbstverständlich die Datenschutzauflagen.
Studieren Sie die 5S-Punkte und versuchen Sie, Möglichkeiten zu finden, diese den Mitarbeitern zu verdeutlichen und mit ihnen Anwendungspunkte abzuleiten. Identifizieren Sie dann geeignete Messgrößen, um die Arten der Verschwendung und die Verbesserungsmöglichkeiten bei den 5S zu erfassen. Diese sind abhängig von der untersuchten Situation, Beispiele gibt Tabelle 2.
Im besten Fall führen Sie die Aufnahme mit den betroffenen Mitarbeitern durch. Suchen Sie das Gespräch mit den Mitarbeitern und hinterfragen Sie aktuelle Zustände. Arbeiten Sie mit offenen Fragen. Scheuen Sie sich bitte davor, sich selbst die Antworten zu geben, denn das wirkt sehr seltsam und meist kontraproduktiv im Team. Vergessen Sie nicht, was es heißt, zu moderieren. Nehmen Sie sich heraus und leiten Sie nur an. Beobachten Sie die Prozesse und Abläufe und machen Sie sich dabei Notizen.
Überlegen Sie, wie Sie die benötigten Daten passend zur Bestandsaufnahme aufbereiten können. Hierbei gilt ganz besonders: "Ein Bild sagt mehr als 1000 Worte". Achten Sie darauf, die Informationen so einfach wie möglich aufzubereiten z.B. mit Whiteboards oder Flipcharts, das sichert Ihnen die breite Unterstützung Ihres Teams.
Bestandaufnahmen können abhängig vom Umfeld sehr unterschiedlich ablaufen. Tabelle 2 zeigt einige Beispiele skizzenhaft auf.
Büroschreibtisch |
Linie |
Produktionszelle |
Logistik |
|
Beispiel: Darstellung von Bearbeitungszeiten pro Einheit |
|
|
Mögliche Messgrößen für die Bestandsaufnahme |
|||
Anzahl der Schriftstücke auf dem Schreibtisch |
Ausschuss |
Werkzeuge am Platz |
Beschädigungen an der Ware |
Anzahl Vorgänge in Bearbeitung |
Bearbeitungszeit |
Werkzeuge i.O. |
Rücksendungen |
Bearbeitungszeit |
Rüstzeit |
Verschmutzungsgrad |
Versendung falscher Artikel |
Zeit zum Wiederauffinden und Bearbeiten von Vorgängen |
Transportzeit |
Hebevorgänge / Positionierungen von Werkstücken |
Lagerunstimmigkeiten |
Wartezeit wegen Hardware / Software |
Nacharbeit |
Laufstrecke pro Bearbeitung |
Durchlaufzeiten |
Sofort weiterlesen und testen
Erster Monat kostenlos,
dann 24,95 € pro Monat
-
Know-how von über 1.000 Profis
-
Methoden für alle Aufgaben
-
Websessions mit Top-Expert:innen
Verstehe den Titel nicht wirklich
23.11.2020
Leider sehe ich nicht wirklich den Zusammenhang des Titels. Letztendlich ging es um die 5S Methode, der Titel hat aber, zumindest mir, suggeriert, dass es um ein spezielles 5S für einen KVP ging. Okay geschenkt, aber weiterhin sehe ich im Text einige aus meiner Erfahrung Lücken. Bei einem 5S im Office Bereich (wird hier ja oft angesprochen) sollten aus meiner Erfahrung die größten Potentiale angesprochen werden: Die Datenablage und das Mailpostfach.
Ein nettes Einsteigerspielchen könnte sein, lassen sie mal das ganze Team einen bestimmtes Dokument auf dem gemeinsamen Laufwerk suchen und messen die jeweilige Zeit. Hier können durch eine sinnvolle Struktur und Namenskonvention riesen Erfolge durch Standardisieren und Sortieren gehoben werden.
Ähnliches gilt für die überquellenden Mailordner, abgearbeitetes kommt ins Archiv, offenes bleibt im Eingang oder ähnlich.
Meiner Erfahrung nach helfen solche Maßnahmen wie, du hast aber zu viele Kugelschreiber oder Bleistifte nicht weiter, zu mal ja viele Firmen mittlerweile haben eh viele Firmen eine Cleandesk Regel. Aber z.B. ein Tipp, Rechtshänder sollten ihr Telefon (falls überhaupt noch vorhanden) links anordnen, Linkshänder ihres rechts. Wenn gefragt wird warum - versuch mal eine Notiz zuschreiben. Das war bei uns immer ein gewisser Opener für solche Schreibtischoptimierungen. Oder die kurze Info am kleinen Drucker wie jetzt da das blöde Geschäftspapier eingelegt werden muss.
Vielen Dank Herr Böll für…
24.11.2020
Vielen Dank Herr Böll für Ihre konkreten Anregungen zum Umsetzen von 5S im Büroalltag!
5S ist ja eine Methode, die für nahezu alle Bereich eingesetzt werden kann - da sind in einer allgemeinen Beschreibung keine Details möglich, rein schon aus Platzgründen. Umso schöner, wenn solche Anregungen aus dem Leserkreis kommen!
Der Bezug zum KVP sollte kein "anderes" 5S implizieren. Vielmehr sollte der enge Zusammenhang bereits im Titel verdeutlicht weren - schließlich sind ja gerade das vierte und fünfte "S" der Kern des KVP.